Precision and safety are at the heart of the assembly of safety components for car chassis. Our assembly machines and systems are used to assemble control arms, tension struts and other chassis components such as sway bars or outer joints. Both joints in POM or cover design and solutions with plastic or steel housings can be installed.
Before the actual assembly, the housing and ball studs are measured. Greasing, press-fitting and, depending on the technology, ultrasonic welding or roller burnishing are typical processes in this assembly. After the torque test, the pivot side is greased and the bellows and the two expansion rings are fitted. In addition to the installation of ball joints in an additional module, rubber-metal bearings can also be pressed in as an option.
The turnkey CONCEPT assembly machine works according to the rotary indexing principle and can include up to 24 process stations. Our designers and developers pay attention to optimum space utilization, effective cycle times and, if required, fully automatic and reliable feeding of all the necessary components.
Flexible systems with a modular design and a defined range of types are constructed from a network of interlinked individual stations. Interlinking of the system parts with “2-level” conveyor belt. The workpiece carriers are returned to floor level. The result is effective use of space and room.
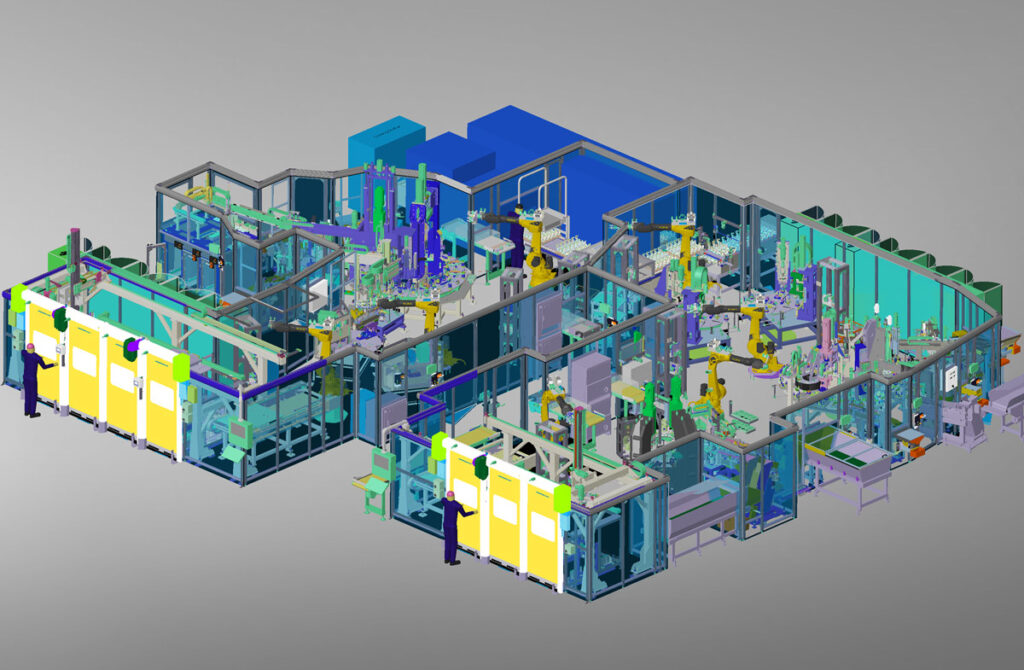
Axle carrier assembly with component handling via robot (from station to station) and automatic feeding of the rubber bearing elements with subsequent assembly (press-fitting).